An all too familiar story…
Although being a global leader in end-to-end solutions and services for the aggregate, mineral processing and metal refining industry, Metso’s documentation process was inefficient and overly complex. Prior to its merger with Metso and when its digital transformation began, Outotec produced technical documentation in MS Word for over 260 products and multiple product lines.
As the manuals were in doc-format, subject matter experts (SMEs) would often make a copy of the manual set to add comments and edit content. With multiple reviewers each making their own copy, the technical writer was soon faced with several sets of the manual each containing comments, sometimes contradictory, that needed to be compiled and merged into one coherent document. This process worked, but it was tedious, time consuming and prone to human errors.
It was clear that something had to be done. This was when Metso’s technical documentation team jump-started an initiative with the help of Etteplan, to migrate their content into the DITA-XML open standard. Metso also leveraged MadCap IXIA CCMS' component content management system (CCMS) to create, manage, standardize, collaborate, review and publish personalized content from a centralized work environment.
Let’s take a closer look…
Metso has multiple product lines, some of which were created organically, and some inherited from acquisitions. Each one of these product lines has its own way of working; therefore, all the user manuals require customization at some point.
In an attempt to standardize the technical documentation process, Metso created a documentation concept describing the manual’s purpose and required content. The documentation concept also contained top-level structure, general guidelines and user instructions. Additionally, Metso implemented harmonized Word templates as well as style guides for content and illustrations. They also provided instructions on how to use these templates to their technical writers, reviewers and SMEs.
To support hundreds of thousands of documents per delivery, Metso implemented two separate document management systems, one for equipment deliveries and one for plant deliveries. This of course added another layer of complexity.
So what’s the problem?
The size of the manuals consisted of hundreds, if not thousands of pages that simply could not be supported in Word. To get around this, each document had to be split into 10 individual chapters. Each chapter contained its own document number and with each delivery, an unnecessary nine new documents were added.
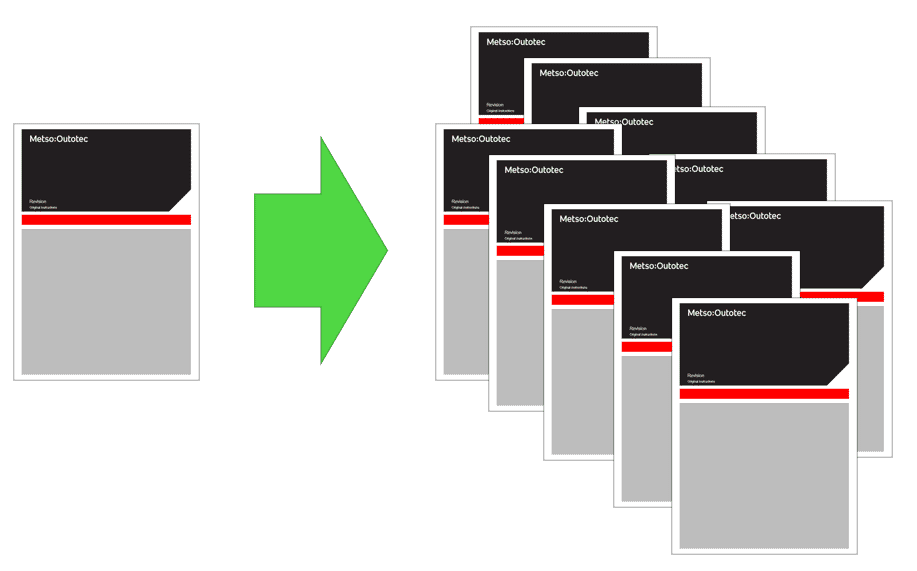
To further complicate things, because the reviewers made their own copy of the manual set, the technical writer now had three or four sets of manuals with comments they needed to go through. Instead of focusing on the actual content of the manual, the technical writers spent an enormous amount of time cutting and pasting text from older deliveries to a final version of the manual. They also spent a significant amount of time on desktop publishing related tasks.
“While working with Microsoft Word was bearable, it was not really something that you would expect from a technology house,” says Jouni Lehtelä, Senior Technical Documentation Specialist at Metso. “There was a lot of high-tech knowledge within our company, but we were still creating content in Word.”
The tipping point…
There were multiple factors that pushed Metso toward structured content, but two really stood out. First and foremost was the overall transition within the industry toward digitized structured content. While the mining industry is quite conservative in content delivery, i.e., everything is delivered in print, Metso understood that digitalization will eventually affect them just the same. Things like AI, connected analytics and remote monitoring would soon be upon them, and they needed one secure gateway for all this digital content to stay ahead of the curve.
Secondly, was the promise of cost savings. Not only was Metso interested in saving a certain amount on annual expenditures, it was also considering what could be done with the hours saved by the increase in efficiency. In other words, the time spent on cutting and pasting and desktop publishing could be better used for creating quality content and intelligent delivery instead.
How did Etteplan help migrate legacy content?
Although Metso has in-house resources, obviously migrating thousands of manuals into structured DITA content was not up their alley. This is when Etteplan came into play.
Most of Metso’s technical writing was outsourced. They already had technical writers from Ettleplan and other organizations. These resources have well over a decade of technical writing expertise and experience with writing specifically for Metso.
Etteplan’s experience with Metso’s product lines allowed them to take the lead to migrate Metso’s legacy content into DITA structured content. The result was a seamless plan and execution.
What was MadCap IXIA CCMS’ role in this whole process?
Instead of passing around complete Word-based manuals, MadCap IXIA CCMS provided a centralized work environment where individual topics could be created, edited and reviewed. Componentizing the content reduced the number of manuals that needed to be managed from 10 to just one. Additionally, the metadata no longer had to be created manually. It is now compiled automatically using Oxygen XML Editor through MadCap IXIA CCMS; thereby, mitigating the possibility for errors.
This was all fine and dandy, but Metso’s products are not standardized at all. They are not only configured to order, but they’re engineered to order as well. This means that with any given delivery, anything could change in the manuals. The traditional way of structured documentation consisting of single-sourcing and fixed conditionals would not have been suitable for Metso.
For example, if Metso had 10 deliveries scheduled at the same time with different content within each manual per delivery, handling this in the traditional way would not have been possible. It would have ended up in the vicious cycle of revising and editing individual topics.
The only viable solution to get around this was MadCap IXIA CCMS' Dynamic Release Management (DRM) module that is designed to support different product models and customer-specific variants.
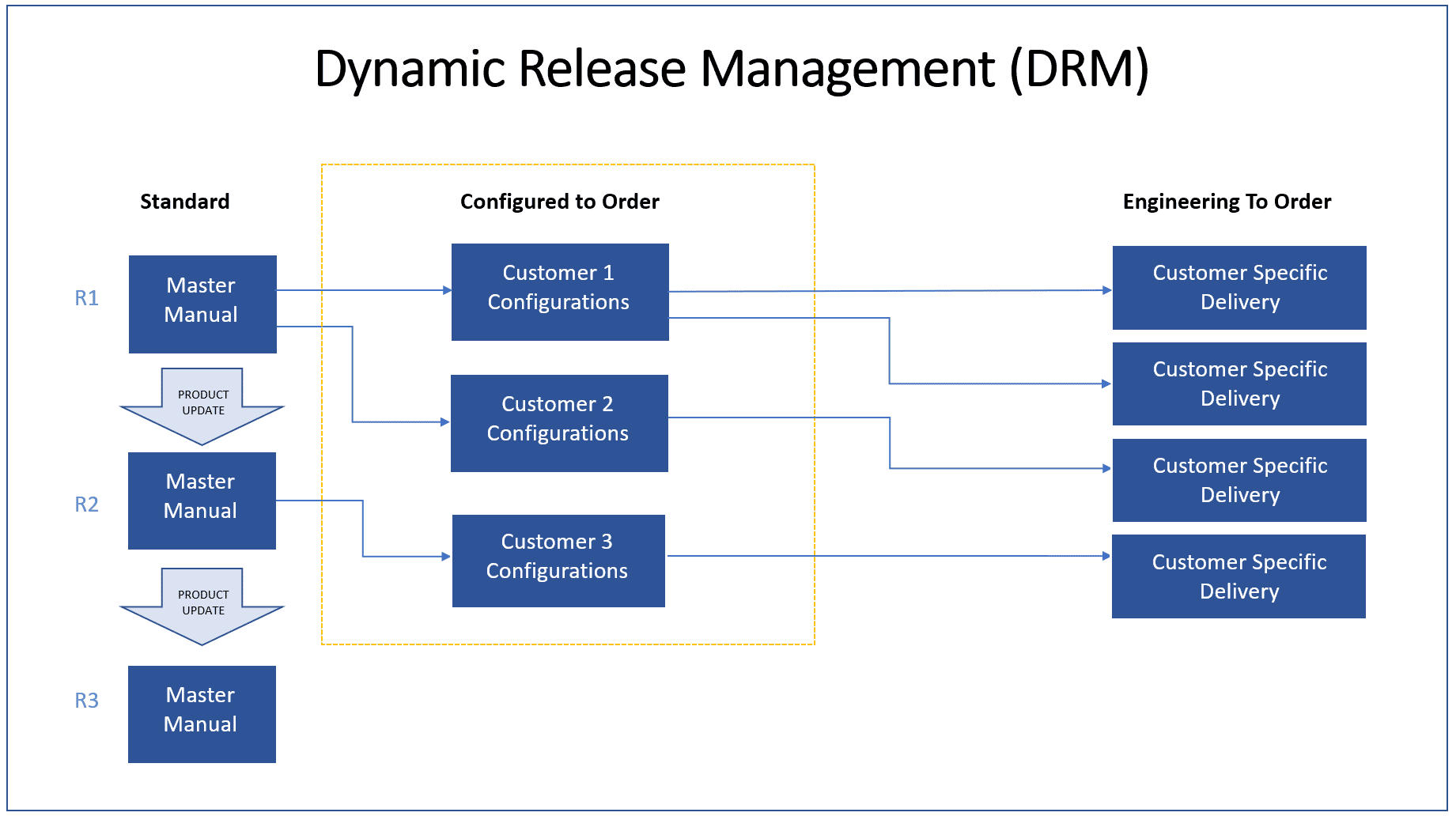
After migrating to structured content, Metso created a master manual consisting of all possible options and configurations for a specific product. Obviously, there are product updates which means that the master manual must be updated periodically.
“With some products, it’s enough to configure the output from the master manual, but quite often we have multiple simultaneous deliveries from the same content and each delivery has something that is customer specific,” says Jouni. “The DRM module enables us to use the same shared content throughout products that are configured to order and engineered to order, and DRM allowed us to add or remove content without affecting the master manual.”
Show me the benefits!
What has Metso gained so far with this transition? Its technical writers and reviewers are much more efficient. Instead of having to go through 700-page manuals to try to figure out what has changed from the previous revision, they can now review only the topics that have changed.
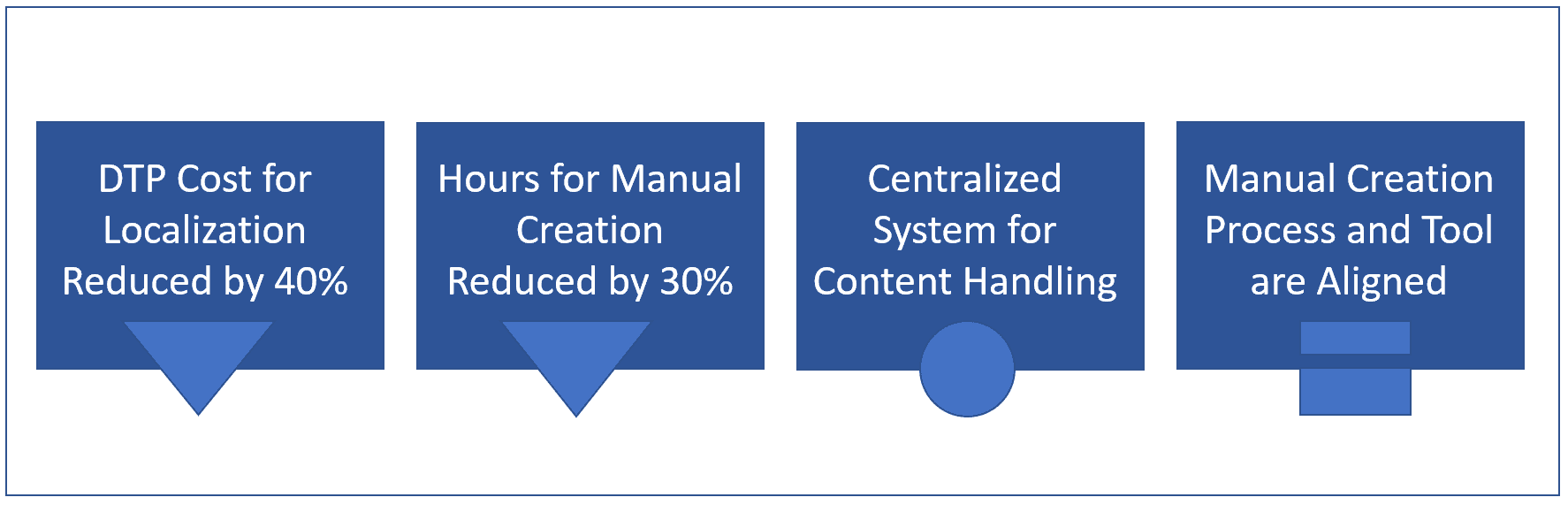
Before digital transformation, Metso had one equipment manual that was represented by 10 different chapters. This caused the desktop publishing for localization to be quite high. Metso managed to cut this cost by 40% annually. Considering that the annual cost for localization is over six figures, this represents a significant amount of savings indeed.
The time it took to create the manuals was also reduced considerably. The technical writers no longer had to work with 10 different manuals and workflows. This represented an efficiency gain of 30% for the most popular Metso product.
Metso now has a centralized system for content handling. This means no more network drives that contain fragmented content. Everything is located in one repository where current or earlier revisions are stored. And lastly, the process for creating manuals and the tools to produce them are finally aligned.
Increased efficiency, cost savings and more control over the entire documentation workflow proves that Metso made a sound decision to move toward structured DITA content managed through IXIA CCMS’s centralized component content management system.
This blog was originally presented at ConVEx Tempe 2022 by Jouni Lehtelä from Metso. Read more about ConVEx conference, and sessions highlights, including sessions by Rocket Software, and the IXIA CCMS team here.